Learn More

Pipeline Dents: Risks, Detection, and Repair with Composites
Pipeline dents are a common integrity challenge in oil and gas transmission systems, often caused by excavation damage, environmental impacts, or improper handling. Left unaddressed, dents can lead to high-stress concentrations, cracking, and costly operational disruptions. Assessing dents properly—considering depth, location, and the presence of gouges or corrosion—is critical to ensuring long-term pipeline reliability.
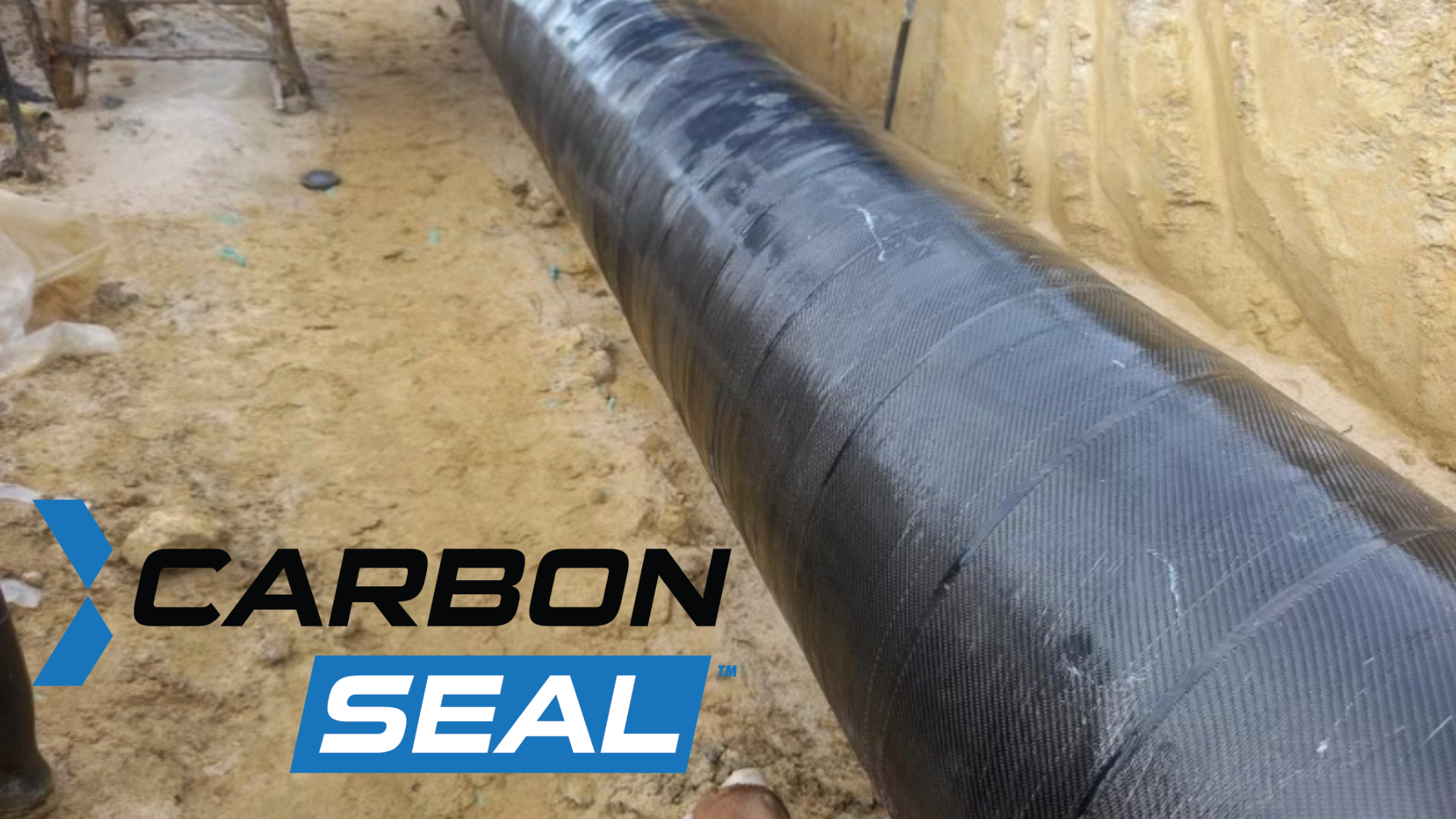
Combating Pipeline Corrosion: The Benefits of Composite Repairs
Pipeline corrosion is a persistent threat. With over a quarter of pipeline incidents in 2023 caused by corrosion (PHMSA), it’s important to find long-lasting, compliant repair solutions. Composites have become a widely accepted repair method for corrosion in the pipeline industry. With benefits like reduced downtime, corrosion resistance, and cost-effectiveness, they are a great alternative to traditional steel sleeve repairs. Read our latest article to learn more about the advantages of composite repairs for pipeline corrosion!